GEMBA
Making Business Better
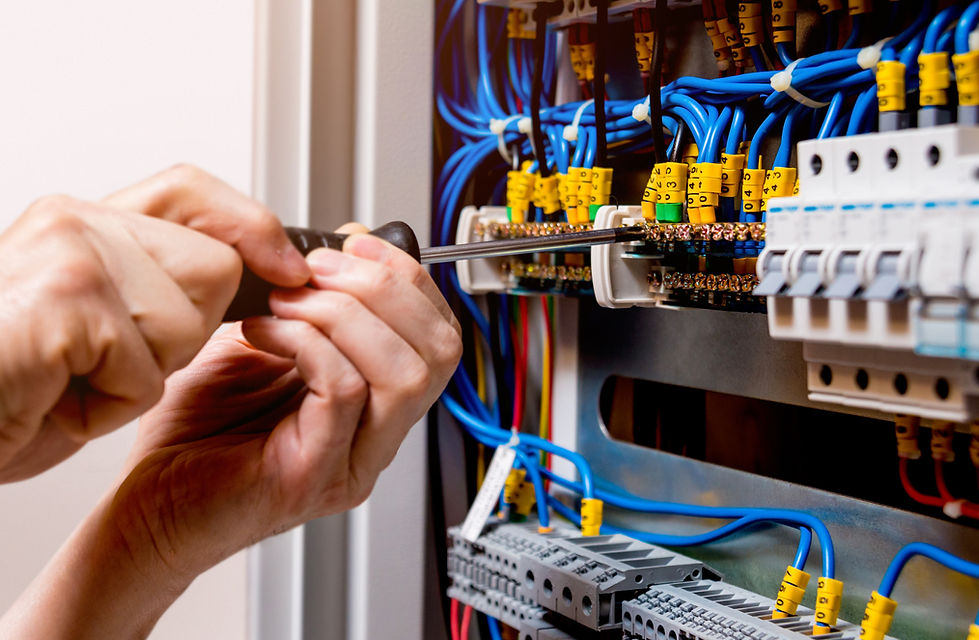
Human Error Reduction Program
We developed what you need; a practical scientific approach to human error reduction and prevention that combines quantitative and qualitative methodologies, easy to use tools and comprehensive training courses. It is the overall solution for achieving human reliability at your site. Our program provides you with everything you need to understand your current situation and fix it once and for all, from a psychological and behavior modification perspective.
The Human Error Reduction Program is composed of six phases, each of them playing an important role and implemented based on your need, which means that our system is adaptable to each organization’s needs and culture. Our Human Error Reduction System is the missing link between quality and productivity and is 100% effective when fully implemented.
Philosophy
We believe people go to work intending to do a good job. When mistakes happen, we tend to oversimplify the situation by fixing the blame and not the problem. In Human Error Solutions we work towards results. Our methodology was designed to cover everything that you need to reduce and prevent the human error rate at your workplace. We know what works and what does not when trying to create an error-free environment; a human error could not be eradicated with a trial and error approach.
Why?
Human error is known to be the primary cause of quality and production losses in many industries. Regulators around the world are much more hyper-attentive to human error events; therefore, a human error is no longer an acceptable cause. Human error explains the what, but it does not solve the why. Our human error reduction training is focused on finding, and fixing, the why.
How?

1. Initial Diagnostic Assessment & Workshop
-
By implementing a scientific approach, a formal diagnosis is performed within the organisation to identify the underlying causes of human performance deviations and assurance responsible data-driven action plan. Human Error Rate is established as pre-measured for continuous effectiveness measurement and tracking and trending.
2. Training Events, Educational program & Tools (Training Roll-out)
-
The human is sophisticated “equipment” and to able to modify behavior, external and internal components need to be understood. We develop and implement a customized educational program based on our initial assessment findings, which provides employees the necessary knowledge and practical tools that will allow them to incorporate mitigation strategies into existing and new processes.
-
We will also provide information that explains the underlying reasons for why humans are making mistakes and how can prevent these errors from occurring at all levels within the organization.
3. Human Reliability Assessment
-
We go deep into two types of risk-based assessments that are performed to identify specific and critical areas of concern. One is the Operation Control Error Prediction (OCP), and the other is the Cognitive Load Error Prediction (CLP); both are performed within a week or less, depending on the magnitude of the client’s operations and scope of the project.
-
At the end of each evaluation, a complete report with risk areas, the rationale for each risk and recommendations are submitted.
4. Implementation phase
-
Planning: The plan addressing the specifically identified areas, developed in conjunction with site members is established to assure implementation and continuity.
-
Coaching & Effectiveness Mentoring: It could be live or remote, to ensure the effectiveness of the recommendations to be implemented. This Phase includes the analysis of the quantitative data, metrics, and KPI’s.
-
Implementation efforts will be determined using objective prioritization techniques. Timeline and efforts will depend on Phase I findings and results.
5. Culture & Collective Behavior Modification
-
HES approach Explores the psychological dimensions and organizational behaviors, so efforts and direction go to strengthen the organization in core process and reduce non-productive behaviors.
-
By enhancing the corporate culture, communicating expected actions, and focusing on quality, regulatory compliance and efficiency the organization’s results can be, not only practical and efficient but also will increase morale and motivation. All these conditions are responsible for variations in the intensity, quality, and direction of ongoing behavior.
6. Monitor and Trend
-
Metrics and Key Performance Indicators are critical to monitor the progress of Error Reduction and Prevention initiatives. Once all elements of our Program are implemented, a trending and tracking protocol for Human Error Rate and other KPI’s is established to assure attainment of organizational goals.
Human Error Prevention and Reduction
Besides being a regulatory requirement in GMP’s across the world to investigate human error incidents and deviations, human error is also known to be the primary cause of quality and production losses in many industries. Although it is unlikely that human error will ever be eliminated, many human performance problems can be prevented. Human failures start at the design stage. From procedures, training, workplace environment, and documentation, many variables that affect human behavior can be manipulated reducing the likelihood of these occurrences.
It is essential to understand human behavior and the psychology of error as well as understand exactly where the weaknesses of the system are so they can be improved and fixed.
Benefits of implementing our 6 phase Human Error Program
Scientific data has shown that our Error Reduction Program when fully implemented, can reduce an organization’s deviations by 60% in a period from 10 to 12 months; especially if it involves error-prone processes. Our program, not only will keep your organization within the regulatory requirements, but it will also impact your organization’s quality, safety, and profitability by:
-
Having less inventory on hold at site
-
On every “order to manufacture,” your shipment will be on time
-
Productivity improvement and cost reduction by reducing cycle time
-
Reduction in inventory write off (less product waste)
-
Increase in your company’s Overall Equipment Effectiveness (OEE)
-
Minimize unplanned downtime
-
Motivation and moral improvement at site
-
Customer complaints reduction
-
Integration of human factors in manufacturing execution systems design. We can design for any type of process; manual, automated or integrated.
-
Reduction necessary documentation